motor with peripherals. A typical 273 volt battery pack as
used in the Toyota Prius Hybrid (up to 500 volts with the
use of the inverter) weighs around 53 kilograms (117 pounds)
in the latest version. They are typically of a type called
nickel-metal hydride. There is a newer and more efficient
type of battery called lithium-ion, but the cost, so far,
has been prohibitive for automotive applications.
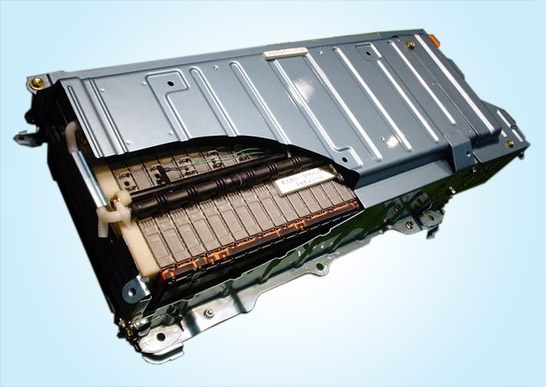
The
Prius battery stack consists of 38 prismatic NiMH modules
connected in series. It delivers a nominal 273.6 Volts and
has a 6.5 Ah capacity. The modules are stacked side by side
and then compressed together in a rigid, non-expandable
structure that prevents expansion from internal pressures.
The complete battery pack consists of the battery stack,
enclosure for structural support and airflow, battery
electronic control unit/monitor, relays, and safety switch.
The weight of the complete battery pack is 53.3 kg. The pack
is horizontally positioned in the trunk of the vehicle,
partially under the back seat. Power electronics (inverter,
DC-AC converter) are under the hood and a blower for moving
air and associated air ducts are in the trunk. Discharge
power capability of the Prius pack is around 20 kW at 50%
SOC with regenerative capability of 14.5 kW at 2C. The power
capability increases with higher temperatures and decreases
at lower temperatures. Active thermal management can improve
power capability at lower temperatures
The
electric motor and controller is a weighty item. As an
example, a 100 horsepower UQM electric motor and controller
weigh around 163 pounds. Then, of course, you need an
internal combustion motor to “top up” the batteries as they
are discharged. If you were to use a very efficient 60
horsepower motor (this motor would only need to cover the
cruise power requirements, not peak power) to take care of
this function, figure in at least 80-100 pounds. So add it
all up and you have around 350 pounds of powerplant to
provide 100 horsepower worth of thrust. Not very compelling
compared to 240 pounds or so for a plain old Continental
O-200. If you take my car, a Honda Insight Hybrid, as an
example, the weight of the battery pack and powerplant has
been offset by extensive use of aluminum chassis elements
|
and plastic or composite
body panels. Our airframes are already pretty light, so it
is hard to compensate for the weight of the hybrid system in
the same way the auto makers do. However, there is an
offsetting weight reduction in that, for the same airplane
range, you are likely to need less fuel to fly the mission.
So perhaps you carry around 50 pounds less fuel in your
two-seater.
THE BOTTOM LINE?
The
hybrid (as we know it today) is not likely to make the
transition from automobile to light aircraft anytime soon.
FUEL CELLS
A real
possibility for general aviation? You have probably read
about several efforts to adapt fuel cell technology for
aviation. So what is a fuel cell? Well, with a typical PEM
(proton exchange membrane) fuel cell, hydrogen and air go in
and electricity and water come out.
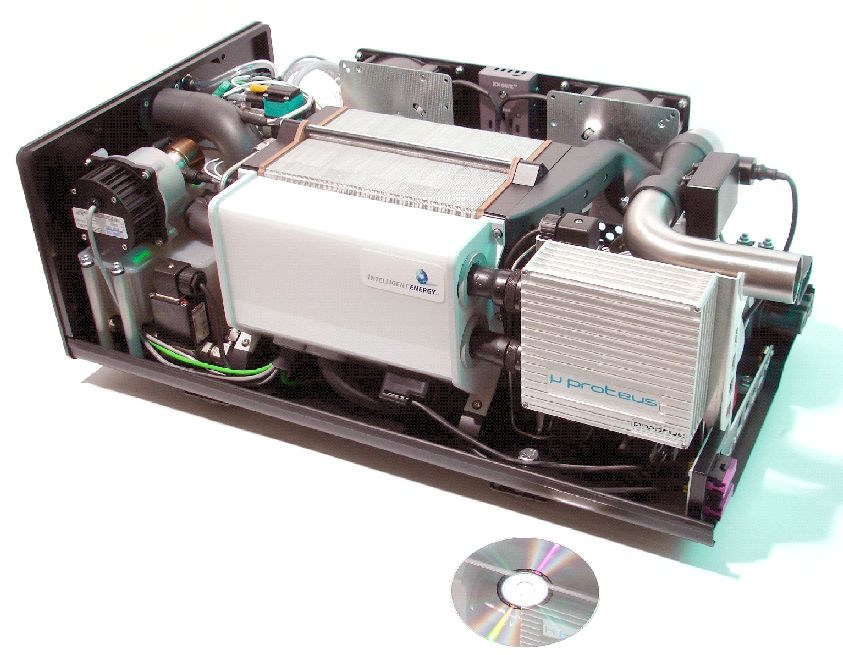
A
typical PEM fuel cell from Intelligent Energy, UK
PEM (proton exchange
membrane) fuel cell, hydrogen and air go in and electricity
and water come out.
Let’s grossly simplify
things and say it's like a battery that is constantly
recharged by putting in hydrogen. It is almost twice as
efficient at generating power as an internal combustion
engine, hence the level of interest and investment by the
auto companies.
Boeing has been researching
the use of fuel cells and has targeted the APU (auxiliary
power unit) as the place where a fuel cell might make sense
in commercial airliners. In order to investigate the
challenges of using this technology in a flying aircraft,
Boeing is building an airplane known as the Fuel Cell
Demonstrator. Based on the airframe of the Diamond Dimona
motorglider, the Demonstrator serves as a flying laboratory
to investigate the integration issues necessary to make a
fuel cell function in flight. The aircraft is expected to
fly by the year 2007.
The Boeing Demonstrator is
configured with a type of hybrid powerplant (not exactly the
same as previously described), with a fuel cell providing
enough electrical
|