Home | Issues |
Articles |
Experimental Aviation Glossary |
Video Hints for Homebuilders |
Q&A |
A Personal View |
Polls
08/08 - Fuel Tank Bonding and Grounding for
Composite Aircraft And
some really good information for the rest of us
By David Gall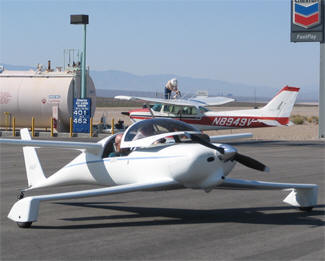
David Gall is an Air Traffic Controller and an EAA member.
Most things written on the subject of fuel tank
bonding are good information, but do not
address the issue from the designer/builder viewpoint of composite aircraft. We
are responsible for constructing our plastic planes in such a manner that the
”normal” advice is applicable. To that end:
Static electricity builds up on the surface of
fuel. Not throughout the bulk of the fuel, but on the SURFACE. The charge is a
result of friction, either due to sloshing within a non-conductive tank, or due
to traveling friction as when flowing through a pipe. When transferring fuel
from one container to another (or from the pump or fuel truck), the fuel
generates a tremendous electrical charge on the way out of the nozzle. The
nozzle acts as a charge separator, dispensing fuel of one polarity while
building a charge of opposite polarity on itself. Just like socks on carpet. If
there is no conductive path for the resulting charge to make its way back to the
nozzle by conduction through wires, it may make its own conductive path through
the air: spark, just like fingers on a doorknob.
The plastic gas cans we buy at Wal-Mart are made
of a conductive plastic. The fuel nozzles at the automobile gas station are
grounded by wires encased in the hose itself. Placing the gas can on the ground
completes the circuit and the can and nozzle are grounded and bonded to each
other. Same for metal cans. Alternatively, placing the nozzle in direct contact
with the can (metal or plastic) will complete the bonding
circuit. However, there is a small risk of spark at the point of contact (just
BEFORE actual contact is made). It is this contact that routinely grounds our
vehicles via the metal-to-metal contact of the filler nozzle to the filler neck
(don't you feel safe?).
The small incidence of refueling fires occurs
mostly in older-style fillers where it is possible for the operator to
unwittingly prevent the nozzle from contacting the filler neck. During the
fueling operation, the static potential between the nozzle and neck increases
(friction, remember) until the voltage is enough to jump the gap in the form of
a spark. Likewise, the fool who fails to remove the plastic gas can from the
back of his truck bed, (liner or not!) can create the same conditions by failing
to make contact between the nozzle and gas can. Or, if there is a bed liner, the
static charge on the gas can BEFORE the nozzle makes contact may make a spark
sufficient to ignite the fuel-air vapors: boom!
The charge built up from refueling is not the
only way to build up a static charge. The almost-non-conductive plastic that our
airplanes are made from makes an excellent charge collector
just by moving through the air - flying. When we land, that charge stays on the
airplane unless a path is provided to dissipate it. That charge will collect and
concentrate in the metal parts of the plane. Similarly, on-board electrical
equipment that is not properly bonded to a COMMON "ground" can set up charges on
the airframe. If your airplane grounding/bonding point is in a flammable mixture
(open fuel tank) at the instant you ground it, the inevitable spark may start a
fire.
Make no mistake, there IS a spark when completing
the grounding/bonding circuit, however small: the low incidence of fires is
because there is not a flammable mixture at the spark location. That may be
because the spark location is remote from the fuel, or because the fuel-air
ratio is not suitable for ignition, or just that the spark is too small (not
enough heat). The typical auto fuel filler neck has too much fuel vapor (too
rich mixture) to ignite from the usually-microscopic grounding spark.
Humidity is a very poor choice of
grounding/bonding conductor. Relying on the relative humidity of the air to
dissipate a static charge may work for the small potentials built up by socks on
carpet, but it is entirely insufficient for the charges built up by the
refueling operation, or even just normal flying or driving. I live in central Florida and I can get a
shock almost every time that I get out of my vehicles if I choose (it depends on
whether I hold onto the door as I get out); the humidity here is not sufficient
to rapidly dissipate the charge that builds up on my car or truck just from
normal driving.
As I said before, static electricity builds up on
the surface of fuel. Inside the fuel tank, this charge is distributed over the
surface of the fuel. But dissimilar charges attract, and if an
oppositely-charged item is brought close to the surface of the fuel, the charge
on the fuel will rush toward it. If the resulting charge concentration is
sufficient, a spark may occur. To prevent this, it is necessary to remove the
charge from the SURFACE of the fuel. Commercial products do this by being made
of conductive materials. Conductivity (among other things) is what
differentiates an "approved" plastic gas can from a milk jug. The
almost-non-conductive plastic that our airplanes are made from does not meet
this criterion.
To dissipate the charge on the fuel effectively
in our plastic airplanes, it is necessary to have a conductor that contacts or
penetrates the surface of the fuel regardless of fuel level. This conductor
should also be connected to the fuel filler neck, fuel filler cap, fuel drain,
fuel line, and any other metal or conductive item that comes in contact with the
fuel, in order to prevent these items from acquiring differing levels of
electric charge.
The conductive circuit need not be entirely
within the tank, but may consist of electrical connections to a common ground or
bonding point. However, the conductor that penetrates the surface of the fuel
absolutely MUST be in constant contact with the surface of the fuel at all
normal operation attitudes and especially at ground parking attitudes regardless
of fuel level (especially at near-empty when the explosion hazard is highest).
This may require more than one wire.
The ONLY solution that satisfies all the foregoing requirements is one
which is permanently installed in the fuel tanks and has a
grounding/bonding-cable attachment point well away from any potential
source |
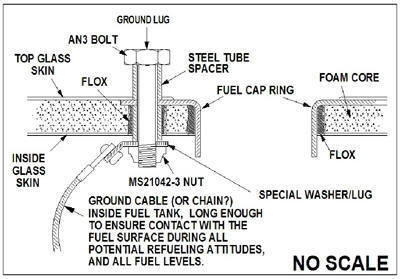 |
of fuel vapor. Ideally, this
grounding/bonding point is accessible before the fuel tanks are opened,
in order to minimize the release of vapors prior to grounding, and the
grounding/bonding cable connection is completed prior to opening the
fuel filler cap. The Central States Association newsletter and others
have published several ideas detailing both new construction and
retrofits for existing composite airplanes. The drawing to the left is a
rendering of one of these, and it should be noted that the
connection should be made prior to removing the cap. Remember, there
WILL be a spark.... |
Comment on this article:
|